Within a thermal management system, heat conducting foils are used as part of Thermal Interface Materials (TIM) to connect heat source and heat sink in the best possible and most efficient way. Depending on the material, they are electrically conductive or dielectric. Their advantage is that they comply to the surface of the hot component. In addition, the design can be adhesive or self-adhesive for easy installation. Learn more.
THERMALLY CONDUCTIVE FOILS
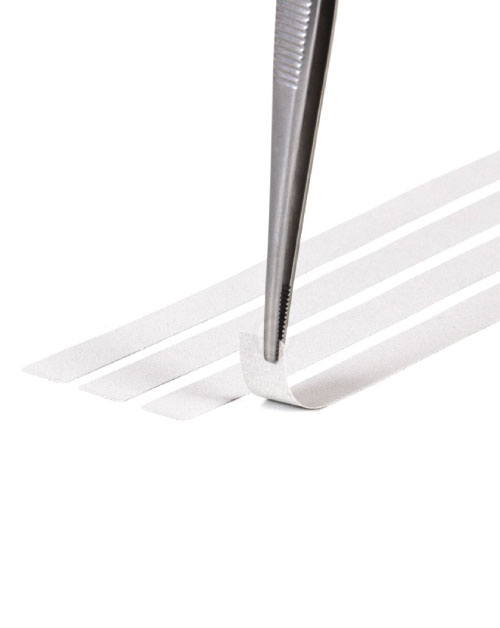
SILICONE FOILS AND FILMS
Under pressure thermally conductive foils achieve an excellent compliance to contact surfaces thus the total thermal resistance is minimized. At the same time a permanent electrical insulation is assured.TYPES:
- Silicone foil fibreglass reinforced
- Silicone foil not reinforced
- Insulating film silicone coated
VARIANTS:
- Material thicknesses of 0.05 up to 1 mm
- Sheet or roll
- Die cut parts
- Kiss cut parts
- With or without adhesiveness
- Reinforcement by glass fiber laminates or Polymide
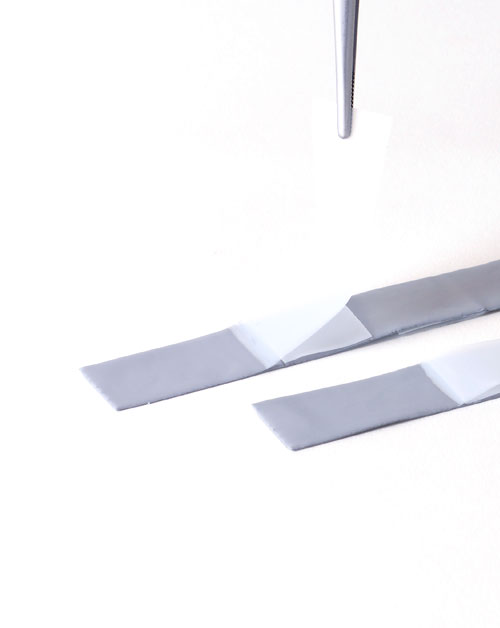
PHASE CHANGE FILMS
During warm-up over phase change temperature, phase change films start filling up surface-specific roughnesses and/or unevenesses and expel any air enclosures from micro structures.TYPES:
- PCM coated polymide film
- Aluminum film PCM coated
- Pyrolytic graphite as a carrier
- PCM film
- Pre-applicable printable PCM compounds
VARIANTS:
- Extremely low thermal resistances through optimum contact
- Silicon-free
- Easy pre-assembly
- Process reliable coating thicknesses
- Pre-applied and dry-to-the-touch printable types
- Ideal replacement of messy thermal grease
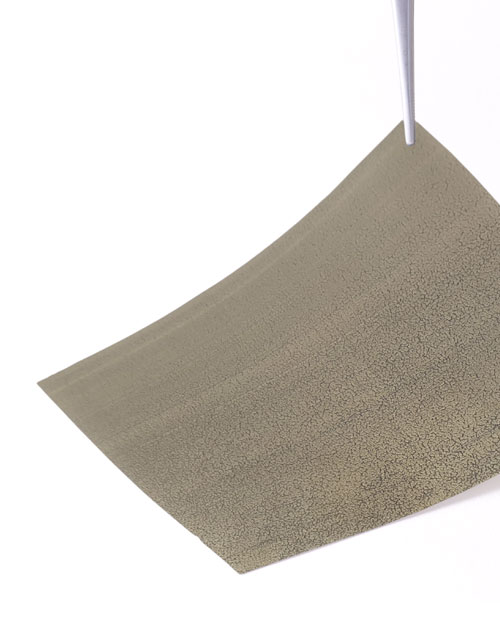
GRAPHITE FOILS
Graphite foils consist of more than 98% pure natural graphite or are processed of synthetic pyrolytic graphite.TYPES:
- Sheet or Roll (natural graphite)
- Die cut parts
- Without or with tackiness
- With or without dielectric films (PEEK, PI, PET)
VARIANTS:
- Thermal conductivities up to 1,950 W/mK in-plane and 25 W/mK in through z-direction
- Heat spreading from hot spots
- Low thermal contact resistance through good surface compliance
- Very low weight
- Silicone-free
- Extreme temperature range up to 400°C
- No dry-up, migrating, run out or pump out
- EMI-shielding through high electrical conductivity as side effect
- 180°C foldable (pyrolytic graphite)
FAQ
Thermally conductive foils, also known as thermal conductive films, are films that are optimally suited to conduct heat from power components in electronic applications due to their high thermal conductivity. The foils are very thin and are usually made of silicone, graphite or phase-change material (PCM). The latter are characterised by the fact that they adapt to the contact surface under pressure and by melting under heat. All types aim to minimise the thermal contact resistance.
Heat conducting foils have the property that they conform to the contact surfaces under pressure. They comply optimally to the heat source and ensure the most effective contact surface by nestling or wetting. This creates a heat-conducting layer that prevents gaps and air holes and therefore works optimally: The heat from the heat source reaches the heat sink through it, and the temperature difference (∆T) between the two layers is minimised. Some thermal conductive films have anisotropic thermal conductivities in the z and planar (x-y) directions, maximising either heat conduction (z) or heat spreading (x-y).
Different thermally conductive films are used depending on the application and purpose.
The most commonly used are dielectric heat conducting foils, for example based on silicone. Their thermal conductivity is maximised by electrical carriers with very high thermal conductivity in the form of specially arranged high-end ceramic fillers such as aluminium oxide, alumimium hydroxide or boron nitride as well as mixtures thereof. Special properties of the film surfaces and the treatment of the surfaces ensure the best possible contact of the heat-conducting films so that dissipated heat can be optimally and quickly transferred to the attached heat sink without great loss – while at the same time providing electrical insulation.
Pure electrical insulating films are also often named as thermally conductive films, e.g. in the form of Kapton MT® or other Poylimides and engineering plastics, whose conductivity is improved by the addition of fillers. They usually have an even higher dielectric strength than insulating heat-conducting films and are easy to process. However, whether they comply well to the surface of the heat source depends on the material composition of the individual insulating foil. In individual cases, insulating foils are therefore combined with special coatings made of phase change compounds or thermally conductive adhesives, among others.
It is widely believed that thermal conductive films are metallic films with electron-based thermal conduction.These are available, for example in the form of natural graphite and pyrolytic graphite as a high-performance version. Here a certain EMI shielding for electromagnetic compatibility is beneficial. This shielding makes it possible to better protect the electronic component from electromagnetic interference from the ambient and vice versa. Due to their flake-like structure, graphite foils have anisotropic thermal conductivities in the foil plane (x-y plane) and perpendicular (z-direction). This allows heat from hot spots to be spread and directed through the foils.
Before a heat conducting film or foil is used, it is often compared with other thermal materials. Whether thermally conductive foils, heat conducting pads or even gap filler pads are more suitable often depends on the type of application and the space to be bridged and the geometry as well as its mission profile. The comparison with a thermal paste often named as thermal grease is interesting.
The differences are obvious: thermal grease is pasty and therefore more difficult to apply. For large quantities, it is only suitable if a process-reliable and repeatable application is ensured. In addition, fluids always have the uncertainty of ageing and doubt of reliability. Thermally conductive foils, on the other hand, can be cut to size as required and are very easy to process. Self-adhesive heat-conducting foils are also often required, whether adhesive on one or both sides, in order to minimize pre-assembly work and to provide a reliable thermal connection between the heat sink and the heat source.
Just like other thermal conductive materials (TIM), thermally conductive foils and films are widely used in many industries:
– Automotive (e.g. engine control units, infotainment, auxiliary heaters, battery chargers).
– Industrial technology (e.g. audio and video components, power supply units, telecommunication systems, hard disc drives, IT components)
– Household appliances (e.g. washing machines, dishwashers, induction ovens)
– Medical technology
– Consumer electronics
– Military and defence industry, aviation and aerospace
Silicone-free dielectric thermally conductive films are often mandatory in the automotive industry, for example, as they conduct heat quickly and efficiently without causing application and adhesion problems of the lack due to silicone outgassing, fogging and deposits.
Private users can find numerous online shops selling standardised heat conducting foils in small quantities through a simple Google search. However, in order to find the optimal solution and heat conducting foils for professional use and for integration into a complex thermal management system, these purchasing channels are not suitable.
This is where we come in: At HALA you will not only find a large selection of heat conducting foils, whether self-adhesive on one or both sides, whether insulating or electrically conductive. We process and supply thermally conductive foils and films as die-cut parts or kiss-cut parts on sheets or rolls.
The best thing to do is to contact us directly – we can consult you free of charge and conveniently online at any time.